Le Lean management est un système d’organisation industrielle initiée dans les usines japonaises du groupe Toyota au début des années 70. L’objectif étant d’améliorer au mieux la performance des processus en exploitant les méthodes, techniques et pratiques déjà à la disposition des managers de la production industrielle.
La mission du Lean Management est d’atteindre l’excellence opérationnelle. Le juste-à-temps, la qualité à tous les niveaux des processus et la réduction des coûts sont ainsi au programme. La flexibilité est l’un des principes fondamentaux du Lean Management.
1ère étape : Initier une démarche
- Stabilité & Standardisation
- Le juste à temps et le JIDOKA (zéro défaut)
- Satisfaction totale client
La pensée Lean :
- Quantifier la valeur du produit du point de vue du client
- Identifier la chaîne de valeur pour mettre en évidence les gaspillages
- Produire seulement ce que le client a commandé
- Rechercher perpétuellement l’amélioration, en faisant la stricte qualité demandée par le client et en éliminant les gaspillages
Les types de Gaspillages :
- Production excessive
- Stocks excessifs
- Défauts, déchets
- Temps d’attente
- Mouvements inutiles
- Déplacements inutiles
- Sous-utilisation des compétences
Pour démarrer sa démarche Lean il est conseillé de mettre en place la méthode 5S qui a plusieurs vertus. Elle est simple à mettre en œuvre, elle fédère les équipes, elle rend visible les progrès et on voit très rapidement les améliorations.
Le 5S c’est : Supprimer l’inutile ; Situer ; Scintiller ; Standardiser ; Suivre.
Chaque démarche de Lean Management est différente, il faut donc s’approprier sa démarche qui sera adaptée à son atelier de production.
« Votre problème est que vous essayez de penser à ce qu’il faut apprendre à vos employés -pour qu’ils travaillent mieux-. Vous n’avez pas besoin de leur apprendre quoi que ce soit. Ce que vous devez faire, c’est aider les opérateurs à rendre leur travail plus facile. C’est cela votre travail. »
Taiichi Ohno
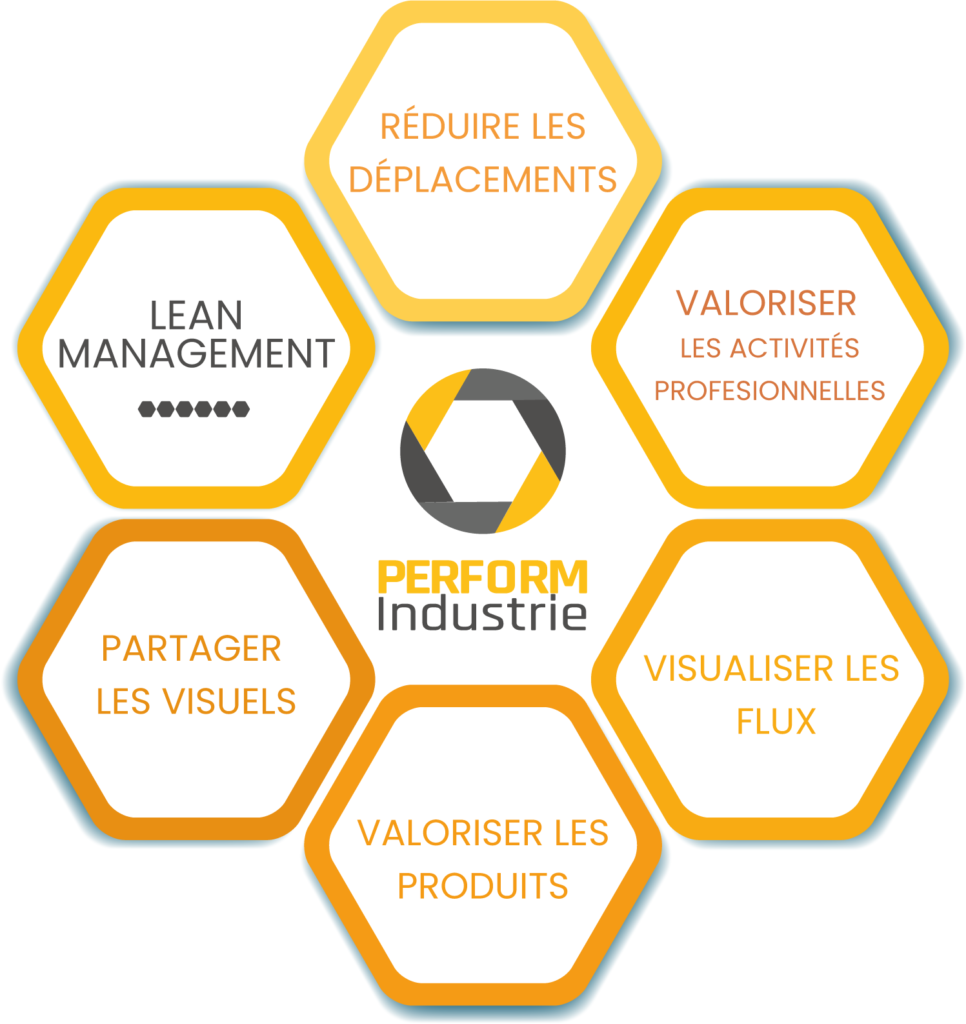
Les objectifs:
Il existes également d’autres objectifs secondaires à cette démarche :
Les risques : S’arrêter ou abandonner la démarche en pleins chantiers Lean. Effectivement une démarche Lean nécessite du temps et de l’investissement, mais si vos efforts sont continus les bénéfices seront à la hauteur de vos attentes.
Notre conseil : Allez-y petit à petit, c’est-à-dire : commencez vos chantiers Lean par espace dans l’atelier. Chaque espaces sera alors réaménager un par un par chantier de 3 jours au plus, ce qui enclavera un cercle vertueux au sien de l’atelier et n’empêchera pas la production.
2ème étape : Améliorer par les flux
Il existe plusieurs types de flux , les principaux sont : flux poussés, les flux tirés, FIFO et flux pièce à pièce.
L’amélioration des flux passe par :
- Un approvisionnement des pièces et composants en juste-à-temps,
- Une meilleure gestion de l’ordonnancement,
- Une gestion des stocks adaptée,
On peut gérer un flux de pièces avec différentes méthodes comme le Kanban ou les doubles bacs par exemple.
Il est important, quand on démarre un chantier d’amélioration, de :
- Faire un état des lieux précis de la situation initiale (en soulevant la principale problématique),
- Projeter la situation finale idéale (quels sont les objectifs que l’on se donne),
- Définir les éléments qui nous permettront de savoir si nous avons atteint nos objectifs,
- Définir les indicateurs qui vont nous permettre de piloter nos actions.
«L’amélioration continue est un état d’esprit qui vise à toujours faire mieux et à ne pas se satisfaire de l’existant »
Vous souhaitez vous former ou former vos collaborateurs sur le Lean Management ?
PERFORM Industrie se tient à votre disposition pour trouver ensemble la formation qui répondra au mieux à vos besoins.